Strato d'usura ad alte prestazioni su pavimentazioni in calcestruzzo
Per la realizzazione di strati d’usura ad elevate prestazioni fisico-meccaniche e di durabilità dei pavimenti in calcestruzzo, AZICHEM propone il premiscelato FLOOR VULKAN
Approccio normativo, prestazioni fisico meccaniche e durabilità del premiscelato FLOOR VULKAN
Strato d'usura: caratteristiche generali
Nella realizzazione di pavimentazioni cementizie, planarità, prestazioni meccaniche e durabilità, sono ovviamente gli obiettivi di primaria importanza. La planarità viene conseguita fin dalla fase di stesura del calcestruzzo, progettando con precisione le quote e posando il conglomerato cementizio con corretti parametri reologici e con l’ausilio di processi meccanizzati che facilitano le operazioni di regolarizzazioni delle superfici (controllo automatico dei parametri del calcestruzzo fresco, vibrostaggiaura ecc.).
Un ultimo decisivo aggiustamento della superficie della pavimentazione industriale viene però affidato alle tecniche di finitura.
La nomenclatura tecnica identifica questo strato di finitura superficiale dei massetti come STRATO D’USURA. Lo scopo dello strato d’usura è quindi quello di migliorare le caratteristiche superficiali della pavimentazione di calcestruzzo, sia per quanto riguarda l’estetica (planarità e uniformità) sia per quanto riguarda le prestazioni fisico-meccaniche e la durabilità fisico-chimica.
Lo strato d’usura realizzato utilizzando prodotti di natura cementizia, viene compiuto con due metodi applicativi:
- a SPOLVERO
- a PASTINA
La stragrande maggioranza dei lavori viene realizzata con il metodo “a spolvero” per la rapidità esecutiva e per le ottimali planarità che si riescono ad ottenere, relegando il metodo a pastina perlopiù alle rampe e alle superfici inclinate in genere, dove la reologia della pastina, ed il suo spessore applicativo, giocano un ruolo determinante per la corretta stesura e per la possibilità di realizzare “rigature” e superfici antiskid con elevato grip sia sulle suole delle scarpe che sulle ruote dei veicoli.
Strato d'usura realizzato con il metodo a spolvero
Sul calcestruzzo posato in opera a quota piano finito, calpestabile ma con “fine presa” non ancora raggiunta, viene applicato a "spolvero o semina" un determinato quantitativo di premiscelato anidro composto da aggregati e leganti. Questo spolvero viene inglobato nel calcestruzzo ancora “fresco” con un’azione congiunta di leggera bagnatura e lisciatura.
L’operazione di lisciatura viene quasi sempre realizzata tramite apparecchiature specifiche a lame rotative (lisciatrici o “elicotteri”), in grado di variare la velocità di rotazione delle pale in funzione della consistenza del calcestruzzo e del livello di lisciatura desiderato.
La scelta del materiale indurente e del quantitativo da applicare è determinata dall’entità dell’azione abrasiva sulla pavimentazione: maggiore è tale azione, maggiore deve essere la resistenza meccanica del calcestruzzo e la resistenza all’abrasione dello spolvero.
Strato d'usura realizzato con il metodo a pastina
Sul calcestruzzo posato in opera a quota meno 5-10 mm dal piano finito, calpestabile ma con “fine presa” non ancora raggiunta, viene applicato, fresco su fresco, un impasto umido (che può anche essere fibrorinforzato) di spessore tale da raggiungere la quota finita. La scelta del materiale indurente e del quantitativo da applicare è determinata dall’entità dell’azione abrasiva sulla pavimentazione: maggiore è tale azione maggiore deve essere la resistenza meccanica del calcestruzzo e la resistenza all’abrasione della pastina.
Il deterioramento dello strato d'usura di una pavimento industriale in calcestruzzo
Nel corso degli anni la realtà esecutiva ha purtroppo evidenziato che i presidi antiusura ed antipolvere a SPOLVERO o a PASTINA sono spesso accompagnati da risultati insoddisfacenti: elevata generazione di polvere, scadenti requisiti di resistenza all'usura ed al logoramento, delaminazione e distacco dello strato d’usura dal resto della pavimentazione cementizia. E' opportuno sottolineare che “la generazione di polvere", oltre ad implicare negative incidenze in termini di durata funzionale della pavimentazione, può comportare aspetti non trascurabili in ordine all’igiene e alla sicurezza dell'ambiente di lavoro: la polvere, generata dal logoramento della pavimentazione, è costituita da minute particelle di natura prevalentemente silicea che, ove inalate per un tempo prolungato, possono essere causa di irritazioni alle vie respiratorie, fino ad arrivare ai più gravi casi di silicosi.
Il precoce deterioramento degli strati d’usura può essere causato sia da materiali scadenti che da tecniche esecutive non conformi alle regole dell’arte. Per quanto riguarda i materiali, per ovviare a queste potenziali carenze, gli strati d’usura sono oggetto di caratterizzazioni e prestazioni di base garantite da standard europei, che andremo ad analizzare attentamente nel prossimo paragrafo e che possono essere un’efficace “chiave di lettura” nella scelta di un prodotto qualitativamente conforme alle attese e alle prestazioni desiderate in fase di progettazione.
I requisiti dei materiali per lo strato d'usura: quale normativa di riferimento?
I premiscelati pronti all’uso in commercio, utilizzabili per lo strato di usura, applicati col metodo a spolvero o a pastina, sono classificabili in base al loro comportamento fisico meccanico e chimico sulla base della normativa europea UNI EN 13813. La normativa UNI EN 13813 definisce le prestazioni di tutti i materiali utili alla realizzazione di massetti: cementizi, a base di solfato di calcio, magnesite e resina sintetica, sia per quanto riguarda lo stato fresco (massetti freschi), sia per lo stato indurito (massetti induriti):
- per i massetti freschi le prestazioni riguardano il tempo di presa, la consistenza e il valore pH;
- per i massetti induriti, le prestazioni riguardano la resistenza alla compressione, la resistenza alla flessione, la resistenza all'usura, la durezza superficiale, la resistenza all'impronta residua, la resistenza ai carichi rotanti, il ritiro e il rigonfiamento, il modulo di elasticità, la forza di aderenza, la resistenza all’urto, la reazione al fuoco, le prestazioni acustiche, la resistenza termica e la resistenza chimica.
Le performance dei massetti induriti vengono identificate tramite sigle alfanumeriche che distinguono varie classi prestazionali.
Per fare qualche esempio su alcuni parametri particolarmente significativi, analizziamo definizioni e suddivisione in classi prestazionali di:
- resistenza meccanica a compressione
- resistenza meccanica a flessione
- resistenza all’usura
- forza di aderenza
Dall’analisi dei diversi parametri si nota che le classi abbracciano ampi range di valori, dovendo comprendere diverse tipologie di massetti (cementizi, a base di solfato di calcio, magnesite o resina sintetica).
A titolo d’esempio, nell’ambito dei cementizi, un prodotto con parametri meccanici espressi dalle sigle:
C70 F7 AR1 B2,0
rappresenta un prodotto con resistenza meccanica a compressione > 70 N/mm2, resistenza a flessione > 7 N/mm2, resistenza all’usura BCA 2 N/mm2, ponendosi perciò ai vertici delle prestazioni ottenibili con prodotti a base cemento.
Si rimanda ovviamente alla lettura della normativa UNI13813 per il completo elenco dei parametri da valutare e per gli opportuni approfondimenti.
FLOOR VULKAN per strati d’usura ad elevate prestazioni fisico-meccaniche e di durabilità
Nelle pavimentazioni in calcestruzzo, anche se rivestite con spolveri indurenti di tipo tradizionale, la "polvere" è il risultato dell'abrasione e del conseguente logoramento dei componenti friabili della pasta di cemento indurita: soprattutto l'idrossido di calcio, definito anche calce libera Ca(OH)₂, notoriamente instabile sotto il profilo chimico, relativamente solubile e intrinsecamente "friabile", costituisce uno dei principali “anelli deboli” dello STRATO D’USURA.
Per la realizzazione di strati d’usura ad elevate prestazioni fisico-meccaniche e di durabilità, AZICHEM propone il premiscelato FLOOR VULKAN, composto da aggregati minerali "duri" (basalti, quarzi e corindone) legati da cemento additivato, opportunamente modificato con microsilicati ad elevato indice di purezza (MICROSIL 90).
FLOOR VULKAN sfrutta le caratteristiche mineralogiche dei materiali più duri presenti nella scala di Mohs, essendo composto, per quanto riguarda la componente “aggregati”, da Quarzi puri selezionati (più duri dei quarzi normalmente impiegati in edilizia, scala Mohs = 7), Corindone (durezza Mohs = 9) e Basalti ad alta durezza (roccia effusiva durissima, tenace e molto resistente all'usura, scala Mohs = 7-8), i quali costituiscono la maggior parte degli aggregati contenuti nella miscela.
La parte relativa alla matrice legante del FLOOR VULKAN, è invece arricchita dai particolari microsilicati MICROSIL 90 che, attraverso “reazione superpozzolanica”* con un cemento particolarmente reattivo in tal senso, conferiscono alla superficie del pavimento corazzato elevatissime prestazioni meccaniche e di durabilità complessiva.
* Trasformazione della calce liberata per idrolisi, in nuovi composti di silicati di calcio idrati, stabili, insolubili e resistenti.
FLOOR VULKAN è un prodotto formulato secondo i seguenti standard normativi:
- CE EN 13813 : Materiali per massetti - Proprietà e requisiti.
- CE EN 1504/3 : Prodotti e sistemi per la protezione e la riparazione delle strutture di calcestruzzo - Definizioni, requisiti, controllo di qualità e valutazione della conformità - Parte 3: Riparazione strutturale
- ACI 201 - 2R 77 - Guide to Durable Concrete: Section 3,4,6 "Recommendations for obtaining abrasion resistant surface".
Il componente MICROSIL 90, contenuto nel FLOOR VULKAN, risponde alla normativa
- CE EN 13263-1:2005 + A1:2009
- Specifiche tecniche FLOOR VULKAN
- Adesione al supporto, UNI EN 1542: > 2,4 N/mm²
- Compatibilità termica, UNI EN 13687-1: 2.4 MPa
- Contenuto di cloruri, UNI EN 1015-17: 0.008 %
- Modulo elastico, UNI EN 13412: 35000 MPa
- Resistenza a compressione dopo 28 giorni, UNI EN 1015-11: 70 N/mm²
- Resistenza a flessione dopo 28 giorni, UNI EN 1015-11: 9.5 N/mm²
- Resistenza alla carbonatazione, UNI EN 13295: dk
- Resistenza allo slittamento, UNI EN 13036-4 (PTV): a secco
- Resistenza all’usura, BCA UNI EN 13892-4 :
- Prova di caduta di una massa con testa sferica diametro 20 mm e massa totale 1000 grammi, UNI EN ISO 6272: altezza di caduta 1600 mm INTEGRO-PASSA, altezza di caduta 1700 mm INTEGRO-PASSA
I parametri tecnici sopra esposti permettono il soddisfacimento della normativa 13813 (Materiali per Massetti _ Proprietà e Requisiti) con i seguenti parametri identificativi:
C70 F7 AR1 B2,0
ponendosi perciò ai vertici delle prestazioni ottenibili con prodotti a base cemento.
I parametri sopra esposti, tutti certificati da laboratori esterni, permettono inoltre a FLOOR VULKAN il soddisfacimento della severa normativa 1504/3 (Prodotti e sistemi per la protezione e la riparazione delle strutture di calcestruzzo - Parte 3: Riparazione strutturale). Questo differenzia in modo sostanziale FLOOR VULKAN da tutti gli altri spolveri/pastine presenti nel mercato, ponendola ai vertici della categoria per quanto riguarda la durabilità nel tempo dello strato d’usura.
La categoria di appartenenza del FLOOR VULKAN alla normativa 1504/3
La categoria di appartenenza del FLOOR VULKAN alla normativa 1504/3, è quella di malta strutturale in categoria R4. Il soddisfacimento dei parametri strutturali della 1504/3 risulta di fondamentale importanza se lo spolvero o la pastina vengono realizzati in ambienti d’esposizione severi dal punto di vista chimico (carbonatazione, attacchi chimici), dal punto di vista meccanico (pavimentazioni sottoposte a carichi statici e stress dinamici) o su pavimentazioni in calcestruzzo fibrorinforzato (specialmente in presenza di fibrorinforzo metallico). La capacità protettiva degli spolveri realizzati con FLOOR VULKAN, nei riguardi del fibrorinforzo metallico, è nettamente superiore a quella degli altri spolveri presenti nel mercato. Ne è testimonianza il superamento del test di carbonatazione insito nella normativa 1504/3, che ricordiamo valuta la resistenza alla carbonatazione di una malta strutturale paragonandola a quella di un calcestruzzo prestazionale MC 0,45.
FLOOR VULKAN: i risultati dei cicli sperimentali condotti nei laboratori Azichem
Cicli sperimentali condotti nei laboratori AZICHEM confermano queste argomentazioni. In questi test provini di malta plastica 4x4x16 cm, confezionati secondo standard EN 196/1, con resistenze caratteristiche di 30 MPa e rapporto a/c 0,58, sono stati totalmente rivestiti con uno spessore millimetrico di FLOOR VULKAN o, in alternativa, identico spessore di strati d’usura tradizionali. I provini sono stati sottoposti a 15 cicli di immersione e asciugatura in soluzioni sature di SOLFATO DI MAGNESIO e CLORURO DI CALCIO, per un totale di 210 giorni di test. I provini sono stati costantemente monitorati in termini di peso e nelle loro dimensioni (contrazioni / espansioni libere) e, al termine del ciclo, nei loro valori fisico meccanici di flessione e compressione.
I provini trattati con spolveri tradizionali hanno subito decrementi delle prestazioni meccaniche di circa il 10% rispetto ai provini trattati con FLOOR VULKAN.
Per quanto riguarda le variazioni di peso e le osservazioni dimensionali, le oscillazioni dovute ai cicli di asciugatura e bagnatura si sono ridotte, nei provini trattati con FLOOR VULKAN, mediamente del 40% – 50%, testimoniando una sensibile riduzione della penetrazione di acqua e di sostanze aggressive.
La funzione di uno strato d’usura su una pavimentazione industriale in calcestruzzo è quella di migliorare le caratteristiche superficiali, sia per quanto riguarda l’estetica (planarità e uniformità), sia per quanto riguarda le prestazioni fisico-meccaniche e la durabilità fisico-chimica dello strato corticale.
Le esperienze di cantiere hanno però messo in luce che le sollecitazioni meccaniche e fisico-chimiche indotte sia dalle condizioni d’esercizio, che da gravose esposizioni ambientali, possono mettere rapidamente in crisi gli strati corticali di bassa o media qualità. In diversi casi lo “strato d’usura” può diventare addirittura “l’anello debole” della piastra in calcestruzzo.
L’approccio normativo ha creato una terminologia condivisa e ha fatto chiarezza sulle classi prestazionali da dichiarare nelle schede tecniche dei prodotti ed è importante che, soprattutto in fase di approccio progettuale, i professionisti del settore valutino con attenzione le prestazioni dei prodotti da inserire in capitolato, in funzione delle classi d’esposizione ambientale e delle condizioni d’esercizio.
FLOOR VULKAN si pone al vertice della categoria fra i prodotti di natura cementizia. Le caratteristiche tecniche che lo rendono unico sono state dettagliatamente spiegate in questo articolo, ed è proprio grazie a queste sue peculiarità tecniche che FLOOR VULKAN viene utilizzato con successo dagli applicatori specializzati da oltre venticinque anni.
VISUALIZZA LA SCHEDA PRODOTTO di FLOOR VULKAN
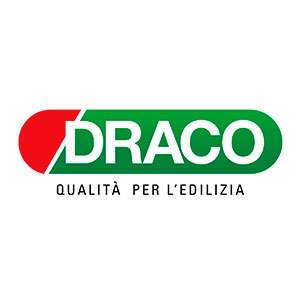
Pavimenti Industriali
Con il topic "pavimento industriale" vengono raccolti tutti gli articoli pubblicati sul Ingenio su queste tipologie di pavimentazioni in calcestruzzo e riguardanti la normativa, la progettazione, l'applicazione, l'innovazione tecnica, i casi studio, i controlli e i pareri degli esperti.