Pavimentazioni per aree logistiche ad alte prestazioni: la progettazione, la realizzazione e i controlli
Le grandi aree logistiche rappresentano una percentuale particolarmente rilevante delle pavimentazioni industriali presenti in Italia.
Le grandi aree logistiche rappresentano una percentuale particolarmente rilevante delle pavimentazioni industriali presenti in Italia.
Essendo soggette a sollecitazioni cicliche rilevanti rappresentano anche un ottimo campo di verifica della durabilità della pavimentazione stessa e nella realtà pratica un collaudo vero del progetto, della qualità dei materiali e della realizzazione in opera.
L’evoluzione tecnologica avvenuta in questi ultimi anni nel settore delle pavimentazioni industriali ha permesso di progettare e realizzare pavimentazioni sempre più performanti, le nuove esigenze tecniche e prestazionali nel settore della logistica richiedono sempre più la realizzazione di pavimenti ad alte prestazioni, l’evoluzione normativa italiana ed europea presenta una velocità e una quantità di produzione di norme nazionali o armonizzate che rendono difficile il lavoro dei professionisti ed in generale degli operatori del settore.
In altri articoli vengono affrontati vari aspetti , dalla progettazione alla realizzazione.
In questo articolo voglio analizzare invece gli aspetti squisitamente realizzativi, ma da un punto di vista critico.
Spesso troviamo innumerevoli indicazioni sulle modalità di realizzazione e di controllo di una pavimentazione, a volte si tratta di una lunga lista di consigli o di aspetti che hanno un importanza più o meno significativa ai fini dell’ottenimento del risultato finale previsto.
In questo articolo si vuole invece concentrare l’attenzione su gli aspetti più significativi, quelli che possono fare la differenza tra una realizzazione di qualità ed una scadente.
Questi aspetti più significativi valgono per tutte le tecnologie oggi utilizzate, dal pavimento tradizionale di buona qualità alle nuove tecniche dei pavimenti senza giunti, con l’impiego di calcestruzzi fibrorinforzati, oppure con l’impiego di pavimenti a basso ritiro utilizzando additivi antiritiro o espansivi, senza dimenticare le pavimentazioni post tese, nelle varie forme realizzative.
Controllo sul calcestruzzo e sull’opera
I controlli in corso d’opera sono uno strumento fondamentale per ottenere un buon risultato.
I controlli più importanti da fare sul calcestruzzo sono:
- La consistenza, da verificare su ogni autobetoniera
- L’omogeneità (visiva) del calcestruzzo in ogni autobetoniera
- Il rapporto Acqua/Cemento
- L’eventuale presenza di bleeding (verifica visiva) da farsi su ogni autobetoniera, nel caso di valori anomali, eseguire la prova secondo UNI)
- Verifica del contenuto d’aria sulla su una prima autobetoniera e su una successiva intermedia
- Verifica delle resistenze meccaniche, da eseguirsi secondo normativa vigente ed in ogni caso con prelievi sulla prima autobetoniera e su una intermedia
- Il tempo di frattazzabilità è facilmente verificabile durante le lavorazioni
- Verifica delle corrette modalità di stagionatura
- Nel caso di calcestruzzi a ritiro controllato eseguire una prova di espansione contrastata il primo giorno di getto e successivamente 1 settimanale
- La verifica del ritiro deve essere eseguita il primo giorno di getto e successivamente 1 ogni settimana
- La verifica dell’umidità residua nel calcestruzzo, quando importante per la programmazione di successivi lavori o applicazioni, dovrà essere eseguita il primo giorno di getto e verificata nel tempo. Successive verifiche potranno essere effettuate solo al variare significativo delle condizioni ambientali o della composizione di progetto.
- Verifica della planarità, ogni giorno di getto nel caso di tolleranze particolarmente restrittive
- Senza dimenticare l’importanza del tempo di miscelazioni del calcestruzzo e la continuità della fornitura
La verifica deve comprendere inoltre pilette , giunti,e armature con:
- verifica delle quote e degli allineamenti, giornaliera
- verifica della posizione dei ferri e del copriferro, giornalmente
- posizione reti gabbie e rinforzi puntuali, giornalmente
Controlli sulla massicciata
Oltre alle note prove di carico è importante verificare le tolleranze delle quote ottenute, che forniranno anche lo spessore minimo della lastra.
Quest’ultimo aspetto riveste una rilevante importanza in quanto le attuali norme vigenti specificano in modo chiaro (anche se personalmente sollevo molte critiche su questo specifico aspetto) le tolleranze degli spessori della lastra e i criteri di accettazione.
Contestualmente alle verifiche degli spessori della massicciata si potranno verificare le posizioni di pozzetti, chiusini, fosse, caditoie e portoni, se correttamente posizionati in bolla, eventuali rinfianchi grossolanamente eseguiti, ecc.
Nella mia esperienza, ho potuto verificare che la costipazione della massicciata risulta essere molto spesso disomogenea (eccessivamente disomogenea) e inoltre sempre carente in particolari punti quali, ad esempio, le zone della massicciata in vicinanza dei pozzetti, delle fosse, dei portoni, in ogni caso dove le attrezzature utilizzate per la costipazione raggiungono con difficoltà tali particolari o dove le stesse attrezzature, per motivi di gestione pratica, risultano essere insufficienti.
Sulla planarità
In questo momento la produzione normativa, a mio avviso, evidenzia una formidabile confusione causata da una modalità che tende ad armonizzare una specifica normativa nel rispetto delle varie esperienze nazionali e, anche, dei relativi rapporti di forza (spesso più commerciali che tecnici).
L’argomento avrebbe bisogno di approfondite tavole di lavoro, non certo di poche righe in un articolo.
Tuttavia è opportuno segnalare che l’attuale normativa e le raccomandazioni di settore evidenziano ben tre differenti criteri di progettazione e relative tolleranze.
Le norme in questione, attualmente vigenti o utilizzate in Italia, sono:
UNI EN 15620 (scaffali)
UNI 11146 (pavimenti industriali)
DIN 18202 (planarità)
DIN15185 (corsie e carrelli)
Deformazioni differite
Un altro aspetto molto importante è la aspettativa delle tolleranze non solo alla fine dei lavori e alla loro consegna, ma le tolleranze di planarità nel corso della vita di esercizio della pavimentazione realizzata.
Le tolleranze fine lavori possono essere anche rispettate, ma durante la successiva stagionatura e nel corso del suo utilizzo la pavimentazione subirà ulteriori deformazioni causat da:
- DEFORMAZIONI DELLA LASTRA SOTTO CARICO
- DEFORMAZIONI DEL SOTTOFONDO
- IMBARCAMENTO (CURLING)
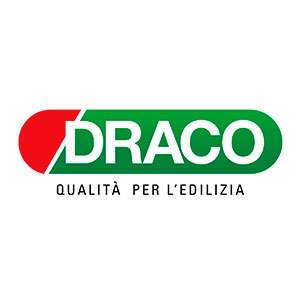
Pavimenti Industriali
Con il topic "pavimento industriale" vengono raccolti tutti gli articoli pubblicati sul Ingenio su queste tipologie di pavimentazioni in calcestruzzo e riguardanti la normativa, la progettazione, l'applicazione, l'innovazione tecnica, i casi studio, i controlli e i pareri degli esperti.