Pavimenti in Calcestruzzo Drenante: riflessioni tecniche e appunti pratici
Un articolo di Roberto Muselli su un'applicazione sempre più importante
L’impiego del calcestruzzo drenante, o calcestruzzo poroso, negli strati di pavimentazione per la mobilita’ lenta sta creando molte opportunita’ nel settore e, al contempo, molte perplessita’ correlate ai numerosi insuccessi di tali applicazioni determinati maggiormente da sgranamenti e da errate valutazioni delle procedure di uso e manutenzione.
La presente vuole essere una breve guida per la valutazione delle attenzioni da porre in atto al fine di non sottovalutare nessun aspetto di tali applicazioni che potranno dare in futuro grandi soddisfazioni.
Il calcestruzzo drenanate e’ un composito cementizio formato da inerti e leganti idraulici caratterizzato da un elevato volume di vuoti. Il tipico dimensionamento di una miscela drenante prevede l’impiego di inerti di media granulometria in pezzatura monogranulare, una miscela di leganti cementizi, l’acqua, gli additivi e l’assenza ( o quasi) di sabbia.
La prestazione di un calcestruzzo poroso si misura in relazione alla sua capacita’ drenanate ed alla sua resistenza meccanica a compressione. Aumentare la capacita’ drenanate significa aumentare il volume di vuoti e, di conseguenza, diminuire la resistenza a compressione. Non essendo un materiale strutturale la resistenza meccanica a compressione e’ indicativa del corretto bilancio fra vuoti e prestazione della pasta e, relativamente a quest’ultima, della prestazione della zona di transizione fra pasta e aggregato. Essendo infatti gli inerti legati fra loro solo dalla pasta cementizia, tutto il lavoro tecnologico nel dimensionamento della miscela e’ svolto in relazione all’aumento della capacita’ adesiva all’interfaccia fra pasta e aggregato e a favorirne la prestazione in opera. In fase plastica va posta particolare attenzione alla vulnerabilita’ della parte corticale esposta a repentina perdita di acqua per evitare fastidiosi sgranamenti superficiali.
L’inerte per il calcestruzzo drenante
La scelta dell’inerte dipende dalla prestazione adesiva e dalla quantita’ di vuoti che il sistema dovra’ possedere.
Relativamente al primo requisito e’ meglio impiegare inerti provenienti da frantumazione piuttosto che inerti tondeggianti, purche’ dotati di buona poliedricita’ cioe’ di un buon coefficiente di forma. Il grado di angolarita’ che caratterizza gli inerti frantumati favorisce il loro accoppiamento reciproco in quanto pone in contatto zone caratterizzate da maggiore superficie rispetto agli inerti tondeggianti. La tessitura degli aggregati e’ preferibile che sia rugosa piuttosto che liscia al fine di aumentare la superficie di contatto fra pasta e aggregato e favorirne l’ingranamento.
In merito al volume di vuoti e’ da osservare che al diminuire della dimensione dell’aggregato aumenta la superficie specifica con conseguente tendenza alla naturale compattazione della miscela. Per questo motivo e’ preferibile che la frazione granulometrica prescelta non presenti alcuna distribuzione, ma sia monogranulare.
In linea di massima con inerti di granulometria compresa fra 4 e 8mm si possono ottenere miscele con vuoti compresi fra il 10 ed il 20% mentre con inerti di granulometria compresa fra 6 e 12mm si possono ottenere miscele con vuoti compresi fra il 12 ed il 25%.
Nel dimensionamento della miscela il volume di vuoti e’ indipendente dalla massa volumica degli aggregati e deve essere almeno il 15%. Sotto a tale valore la struttura intercomunicante dei vuoti non risulta efficace ai fini del drenaggio.
L’impiego di inerti leggeri o caratterizzati da modeste prestazioni meccaniche puo’ sensibilmente ridurre la resistenza a trazione del sistema.
Le resistenze a compressione possono variare fra 12 e 25N/mm2 a 28gg.
La capacita’ drenante accettabile, a seconda del volume di vuoti, varia fra 100 e 750lt/min/m2 oppure fra 0,15 e 1,20cm/sec.
A questo proposito, nel progetto della miscela, e’ bene non trascurare la prestazione attesa dalla piastra in termini di capacita’ drenante posto che, nella peggiore delle ipotesi, il minimo valore 100lt/min/m2 (circa 15% di vuoti) e’ relativo ad una prestazione che non puo’ essere messa in crisi nemmeno dal piu’ violento dei temporali tropicali.
Determinazione del volume di pasta
I metodi di dimensionamento del calcestruzzo drenante piu’ diffusi sono quelli proposti dalla ACI 522R-10, da Zouaghi e da Zheng et al.
Tutti partono dalla valutazione del volume di vuoti in funzione dell’aggregato disponibile o prescelto.
Una volta stabilito il volume di vuoti il proporzionamento della miscela deve procedere secondo due possibili teorie che tengono conto del rapporto fra il contenuto di inerti e cemento in massa ed in volume.
Secondo la teoria piu’ diffusa il rapporto in massa Inerte/Cemento deve essere compreso fra 3,8 e 5,5 mentre la seconda teoria indica che il rapporto in volume Pasta/Aggregati deve essere compreso fra 0,3 e 0,5 tenendo conto, in ambedue i casi, del rapporto a/c (o a/l) tipicamente compreso fra 0,28 e 0,35.
Il secondo approccio e’ piu’ interessante qualora si debbano impiegare aggregati con massa volumica diversa fra loro.
Prestazione della zona di transizione all’interfaccia pasta-aggregato
In fase plastica la pasta avvolge gli aggregati favorendo il loro accoppiamento reciproco.
Una volta indurita la pasta, il sistema sara’ tanto piu’ prestazionale quanto piu’ efficace sara’ l’adesione fra la pasta e gli aggregati e quanto piu’ spessa sara’ la pasta che avvolge gli aggregati.
Valutazione della consistenza effettuata con cono di Abrams_nella prima immagine si vede l'abbassamento di 17cm dopo la miscelazione, la pasta è lucida e l’impasto è coeso; nella seconda immagine l'abbassamento è di 16cm dopo un’ora di miscelazione, la pasta si presenta ancora lucida ma inizia a disidratarsi.
In realta’ l’acqua, essiccando, lascera’ un vuoto in tale zona riconducibile ad una specifica porosita’ del calcestruzzo di importanza predominante per la prestazione meccanica dei sistemi drenanti.
Nel calcestruzzo indurito in tale zona sara’ possibile trovare aria, idrossido di calcio ed, eventualmente, altri prodotti anidri veicolati dall’aliquota di acqua libera.
Tanto piu’ e’ elevato il rapporto a/c e tanto piu’ marcata sara’ tale porosita’ e la presenza dei contenuti sopra indicati con drastiche diminuzioni delle prestazioni meccaniche.
Il cls drenante deve essere progettato e messo in opera cercando il migliore compromesso nella convivenza con la porosita’ sopra descritta.
La diminuzione della dimensione di tale porosita’ avviene attraverso una efficace idratazione del cemento. Considerato l’esiguo contenuto di acqua di un sistema drenante, piuttosto prossimo al valore stechiometrico, e’ possibile procedere in due direzioni: creare un sistema a idratazione controllata oppure impiegare un cemento a rapida idratazione.
Impiegare cementi finemente macinati, disposti ad una idratazione piu’ efficace e rapida, porta ad una difficile gestione del composito e ad un fallimento del risultato dell’opera correlati a riscaldamento della miscela e rapida disidratazione della parte superficiale.
Una buona soluzione e’ quella di impiegare una miscela legante realizzata con l’impiego materiali cementizi secondari (SCM) caratterizzata da tempi di presa piu’ dilatati, congiuntamente ad additivi regolatori dell’idratazione. Nella scelta di eventuali SCM e’ bene valutare la loro influenza sui tempi di presa e sulla produzione di eventuali efflorescenze.
Per aumentare l’efficacia della pasta alla zona di transizione e’ possibile controllare la dimensione di quest’ultima con l’impiego di additivi stabilizzatori dell’aria oppure con l’impiego di additivi a base di Polivinilacetato (VAE Vinyl Acetate Etylene compolymer).
In ogni caso sara’ fondamentale la continua idratazione in fase di maturazione (1) con l’applicazione di efficaci sistemi deputati al contrasto della evaporazione ed, eventualmente, con l’applicazione di speciali formulati a base di Fluorosilicati (2) in grado di trasformare l’idrossido di calcio in prodotti idrati e conferire un efficace consolidamento superficiale.
Un’altra strategia per il controllo dell’idratazione consiste nell’impiego di additivi a base di polimeri super-assorbenti (SAP Super Absorbent Polymer) o di paraffine in dispersione acquosa, denominati ICA (Internal Curing Admixtures). Tali additivi promuovono un rilascio programmato dell’acqua, precedentemente assorbita, in un tempo variabile da 3 a 7gg in base alla loro formulazione. Se da una parte promuovono una efficace idratazione dei leganti nella sezione dei getti, dall’altra introducono dei vuoti non desiderati nella pasta che possono influenzare negativamente le prestazioni meccaniche.
Note:
(1) L’acqua è ancora necessaria per idratare il cemento portland del sistema cemento-polimero. Il lattice polimerico conserva una parte dell'acqua di miscelazione nella miscela; l'acqua viene poi rilasciata al cemento durante il processo di idratazione. La rimozione dell'acqua fa si che il lattice si coalizzi formando un film polimerico. Pertanto, dopo 24 ore di maturazione ad umido per ridurre gli effetti del ritiro plastico, puo’ non essere necessaria un'ulteriore polimerizzazione umida e in realtà non è desiderabile perché il film di lattice ha bisogno di un'opportunità per essiccare e sviluppare le proprietà attese.
(2) L’applicazione in superfcie di Silicati e Fluorosilicati promuove la formazioni di ulteriori idrati in combinazione con l’Idrossido di calcio. Essendo tale attivita’ espansiva e’ necessario che la parte corticale trattata abbia maturato una resistenza a trazione min. 1,5N/mm2. Per questo motivo l’applicazione di silicati come antievaporante va testata e monitorata preventivamente al fine di non generare sfarinamenti e sgranamenti.
L'ARTICOLO PROSEGUE IN ALLEGATO
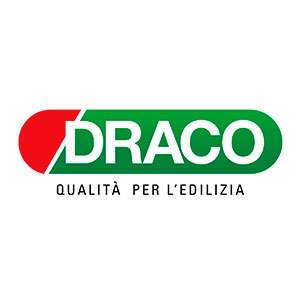
Pavimenti per Esterni
Le pavimentazioni outdoor, che spaziano dalle superfici per terrazze ai camminamenti nei giardini, dai bordi piscina fino alle pavimentazioni...