Per una visione sempre più sostenibile: le malte di cemento con inerti polimerici
Nel presente lavoro, si analizzano le malte confezionate con granuli di polipropilene o di gomma provenienti dalla filiera del riciclo, per poi confrontarle con quelle tradizionali e fibrorinforzate, soffermandosi in particolare sulle prestazioni meccaniche ed ecologiche.
Sono state realizzate diverse tipologie di malta con percentuali di polimeri sostituiti variabili dal 30% all’80%.
Dal punto di vista ambientale, tale soluzione può essere una buona pratica nelle aree geografiche che presentano scarsità di materie prime.
Considerando invece i parametri meccanici, le malte confezionate con inerti polimerici mostrano un’elevata leggerezza e maggiore duttilità rispetto a quelle tradizionali, consentendo una diminuzione della massa dell’interno edificio e una maggiore capacità di dissipare energia unitamente a capacità di isolamento termico.
Articolo presentato in occasione degli Italian Concrete Days 2018 di aicap e CTE
Cement-based mortars with polymeric aggregates
Le malte di cemento con inerti polimerici
1 INTRODUZIONE
Uno dei principali problemi moderni è l’interazione uomo-natura. Circa 800 000 anni fa, nell’atmosfera erano presenti 185 ppm di anidride carbonica, aumentata a 278 ppm all’inizio dell’era industriale.
Da quel momento, a causa dell’operato dell’uomo, la concentrazione di CO2 ha avuto un incremento più rapido, raggiungendo 403 ppm nel gennaio del 2016.
Il calcestruzzo, secondo materiale più utilizzato al mondo dopo l’acqua, con un consumo stimato di circa 1 metro cubo pro-capite annuo, contribuisce al rilascio di anidride carbonica in atmosfera.
Si stima che circa il 5% delle emissioni di anidride carbonica globali sia dovuto proprio alla produzione del cemento (Habert & Roussel 2009).
A fronte di un così elevato utilizzo mondiale e dell’impatto ambientale ad esso legato, unitamente alla problematica di gestione dei rifiuti, è indispensabile cercare di intervenire sul ciclo di vita dei conglomerati cementizi, riducendo il consumo di materie prime naturali e di combustibili, a favore dei materiali riciclati, e diminuendo le emissioni in atmosfera.
È però evidente che non sempre è possibile confezionare calcestruzzi ecologici e con caratteristiche tali da poter essere impiegati nell’industria delle costruzioni.
Per tale ragione, è stata proposta l’analisi eco-meccanica (Fantilli & Chiaia 2013a, Fantilli & Chiaia 2013b, Fantilli et al. 2015), una tipologia di valutazione in cui si considerano unitamente le caratteristiche ecologiche e meccaniche dei compositi cementizi.
Il presente lavoro è basato proprio sull’analisi ecomeccanica di malte cementizie, nelle quali una parte degli inerti è stata sostituita con poli-propilene o gomma provenienti dalla filiera del riciclo.
Nei seguenti paragrafi, si descrive in primo luogo l’impatto ambientale legato alla produzione dei conglomerati cementizi, dopodiché si procede all’identificazione delle possibili soluzioni per la riduzione di tale impatto. Si descrive quindi una campagna sperimentale condotta al Politecnico di Torino, i cui risultati sono studiati con l’analisi eco-meccanica.
2 L’IMPATTO AMBIENTALE
2.1 Il mercato del cemento
Nel 2016, i consumi mondiali di cemento sono aumentati dell’1,7% rispetto all’anno precedente, raggiungendo 3,97 miliardi di tonnellate.
Il 58% di tale quota è dovuta al mercato cinese che nel 2016 ha consumato 2,31 miliardi di tonnellate di cemento, seguito dal mercato indiano con 256,8 milioni di tonnellate. L’Europa occidentale ha avuto un aumento dello 0,9%, anche se i consumi nazionali sono diminuiti del 4,8%.
Basandosi sui dati del Ministero dello Sviluppo Economico e dell’ISTAT, si evince che il consumo di cemento pro-capite è diminuito, assestandosi a 308 kg/abitante nel 2016. Ciò è dovuto a una diminuzione dei consumi nazionali, non bilanciata dalla riduzione del numero di abitanti.
Per quanto concerne la produzione di cemento, nel 2016 in Italia è diminuita del 7,2% rispetto all’anno precedente, assestandosi a 19,3 milioni di tonnellate, con un forte decremento al sud e nelle isole (pari al 10%).
Per quanto riguarda invece la produzione del cemento nel resto del mondo, nel 2015, la Cina ha rappresentato il 58% della produzione globale del cemento, seguita dall'India (6,8%), dall’Unione Europea (4,4%) e dagli Stati Uniti (2,7%) (Janssens-Maenhout et al. 2016, AITEC 2017).
2.2 Consumi energetici e impatto ambientale
Nel processo produttivo del cemento risultano essere di fondamentale importanza gli aspetti riguardanti i costi energetici, le emissioni e il consumo di materie prime.
La massa del conglomerato cementizio è normalmente costituita dal 10% di cemento e dal 90% di acqua e inerti.
Il processo di estrazione delle materie prime per la produzione del clinker e degli aggregati provoca un impatto diretto sul territorio, di natura prevalentemente paesaggistica. In Italia, sono attive 5592 cave e l’estrazione di sabbia e ghiaia, nel 2012, si è attestata a circa 50 milioni di metri cubi, rappresentando il 62,5% di tutti i materiali cavati sul territorio nazionale (AITEC 2016, AITEC 2017, Nanni et al. 2014).
Il processo di estrazione delle materie prime, il confezionamento del conglomerato e il trasporto dello stesso in cantiere necessitano di una scarsa quantità di energia ed emettono una mole discreta di anidride carbonica.
La maggiore quota di emissioni e consumi riguarda invece la produzione del cemento. Il ciclo produttivo di tale legante incide sull’ambiente tramite emissioni dirette e indirette di gas serra. Infatti, il riscaldamento del calcare per la produzione dell’ossido di calcio (calcinazione), rilascia direttamente CO2:
CaCO3 →CaO + CO2 (1)
Tale reazione rappresenta circa il 50% di tutte le emissioni prodotte dalla produzione di cemento e nel 2015 ha contribuito per circa il 4% alle emissioni globali.
Mentre l’impiego dei combustibili fossili, quali carbone, gas naturale o petrolio, per riscaldare il forno provoca emissioni indirette di CO2. Questo rappresenta circa il 40% delle emissioni del ciclo produttivo del cemento, contribuendo anch’esse per circa il 4% alle emissioni globali di CO2. Infine, l'elettricità utilizzata per alimentare i macchinari e l’energia per il trasporto finale del cemento rappresenta un'altra fonte di emissioni indirette, pari a circa il 5-10% delle emissioni del settore.
Si stima che per ogni tonnellata di cemento Portland prodotto si impieghino dai 60 ai 130 kg di combustibili e circa 110 kWh di energia elettrica, emettendo dai 900 ai 1100 kg di CO2 (circa 220 – 240 kg ogni metro cubo di conglomerato prodotto).
I consumi di energia elettrica rilevati nel 2016 sono risultati in calo di circa il 7% rispetto al 2015, attestandosi a valori vicini a 2,3 GWh. L’efficienza degli impianti produttivi italiani comporta un fabbi-sogno medio di 117 KWh per tonnellata di cemento prodotto, un valore in miglioramento rispetto a quel-lo registrato nel 2015 (122KWh), ma comunque al di sopra del valore medio mondiale pari a 110 KWh per tonnellata. Secondo l’ENEA circa il 28% dell’energia elettrica consumata è destinata alla ma-cinazione del crudo, il 22% alla cottura del clinker, il 38% alla macinazione del cotto e circa il 12% è im-piegata per altri usi di servizio, come il funziona-mento dei ventilatori e il riscaldamento del combu-stibile.
Dati meno confortanti riguardano il consumo di materie prime, sceso di circa 4 milioni di tonnellate dal 2013 al 2014, attestandosi a circa 25 milioni e variando leggermente nel 2015. In modo analogo, il tasso di sostituzione delle materie naturali con scarti industriali, salito dal 6,4% al 6,6% dal 2013 al 2014, è diminuito nuovamente nel 2015 al 6,2% (Janssens-Maenhout et al. 2016, AITEC 2016, AITEC 2017, CEMBUREAU 2013, ENEA 2014).
3 STRATEGIE DI RIDUZIONE
A fronte dell’inquinamento ambientale sempre più consistente, negli ultimi decenni si sono cercate soluzioni e strategie per ridurre l’impatto dell’uomo sull’ambiente.
L’European Concrete Platform ha introdotto il concetto di struttura eco-efficiente in calcestruzzo e ha promosso una serie di regole per ridurre il “cement carbon footprint” del 32% entro il 2050 (CEMBUREAU 2013):
- Resource efficiency;
- Energy efficiency;
- Carbon sequestration and reuse;
- Product efficiency;
- Downstream.
Occorre dunque intervenire sulla natura del mate-riale utilizzato, sulla sua produzione e sull’impiego dello stesso nelle costruzioni.
3.1 Resource efficiency
L’unicità del processo e le esigenze energetiche dell’industria cementizia consentono l’impiego di miscele di combustibili, definite alternative, che non sarebbero adatte ad altre tipologie di industrie.
È stato stimato che entro il 2050 il 40% dell'energia del forno potrebbe provenire da fonti tradizionali, mentre il 60% dell'energia necessaria potrebbe essere fornita da combustibili alternativi.
Ciò consente la riduzione delle emissioni di anidride carbonica e un miglioramento del processo di gestione dei rifiuti.
Oltre a intervenire sulla tipologia di combustibile si può operare anche sulle materie prime impiegate nel processo, sostituendone una parte con materiali che contengano calcio, silice, allumina e ferro, come i rifiuti e i sottoprodotti industriali, oppure le ceneri provenienti da altri processi industriali.
L’impiego di materie prime alternative porta alla produzione di differenti tipi di cemento, che hanno proprietà diverse e che condizionano l’applicazione del conglomerato cementizio. È quindi necessario garantire, durante la fase di sostituzione, che le caratteristiche meccaniche del prodotto finale siano quelle desiderate.
3.2 Energy efficiency
Il secondo aspetto da considerare è l’energia consumata durante il processo produttivo del cemento.
La riduzione dei consumi elettrici può essere operata mediante modernizzazioni, riguardanti le tecniche di macinazione, i processi di recupero di calore, le tecnologie di raffreddamento e gli azionamenti a velocità variabile.
È fondamentale l’impiego di energia da fonti rinnovabili, poiché le tecnologie volte alla riduzione del fabbisogno termico e quelle legate alla diminuzione delle emissioni in atmosfera comportano un incremento dei consumi elettrici dell’impianto.
Il processo di clinkerizzazione, che consiste nel riscaldare il calcare a circa 1450°C, richiede una quantità di energia termica che comporta circa il 35% delle emissioni di anidride carbonica dell’intero processo. Rispetto agli anni ’60 del secolo scorso, i consumi degli impianti sono diminuiti grazie allo smaltimento delle centrali umide, all’impiego di tecnologie più moderne e alla concentrazione della pro-duzione in pochi grandi impianti. Nel 2010, l’efficienza energetica era dell’ordine di 3730 MJ/tclinker. Tale valore può essere ridotto a circa 3,3 MJ/tclinker entro il 2050, tramite l’impiego di combustibili alternativi e il miglioramento dei forni utilizzati.
3.3 Carbon sequestration and reuse
Anche utilizzando un impianto produttivo ideale, non è possibile ridurre la quota di CO2 prodotta du-rante la calcinazione. Sono attualmente studiati e sviluppati dei sistemi che sarebbero in grado di cat-turare il 90% delle emissioni, definiti CCS (Carbon Capture and Storage). L’anidride carbonica potrebbe essere trasportata e impiegata come materia prima in altri processi industriali, oppure iniettata e stoccata nel suolo terrestre. La metodologia presenta però al-cuni problemi. Infatti, il costo di produzione del ce-mento potrebbe aumentare dal 25% al 100%, e ciò richiederebbe anche un maggiore quantitativo di energia elettrica, senza considerare che vi devono essere aree di stoccaggio e sistemi di trasporto ido-nei. Un’alternativa possibile è quella di impiegare l’anidride carbonica prodotta per coltivare alghe, da utilizzare come combustibile.
...
L'ARTICOLO COMPLETO E' DISPONIBILE IN ALLEGATO
KEYWORDS: Aggregati polimerici, Fibre di plastica, Prestazioni meccaniche, Prestazioni ecologiche, Analisi eco-meccanica, Unità funzionale.
A Napoli dal 14 al 17 aprile 2021 la terza edizione degli Italian Concrete Days di aicap e CTE.
IL PIU' IMPORTANTE EVENTO TECNICO/SCIENTIFICO SUL CALCESTRUZZO IN ITALIA
Ecco le informazioni per partecipare agli Italian Concrete Days 2020 di aicap e CTE a Napoli
Cementi e Leganti Sostenibili
La sezione INGENIO dedicata ai cementi e leganti sostenibili raccoglie articoli tecnici, normative, casi applicativi e innovazioni per un’edilizia a basso impatto ambientale. Un riferimento essenziale per chi costruisce il futuro.
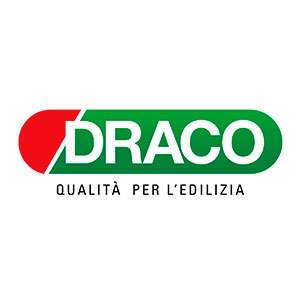
Malte da Rinforzo Strutturale
Con il topic "Malte Strutturali" vengono raccolti tutti gli articoli pubblicati sul Ingenio sulle Malte ad uso Strutturale e riguardanti la progettazione, l'applicazione, l'innovazione tecnica, i casi studio, i controlli e i pareri degli esperti.