Pavimentazioni in calcestruzzo: soluzioni per la corretta maturazione dei getti in estate
Le alte temperature del clima estivo possono inficiare sulla corretta maturazione del calcestruzzo. Come fare? Parola agli esperti di General Admixtures SpA.
Protezione del calcestruzzo giovane in presenza di alte temperature
Realizzare superfici in basso spessore in calcestruzzo in estate: ci possono essere dei problemi?
Pasqualini Alessandro
Il pensiero corre immediatamente alle pavimentazioni industriali o, in generale, alle solette in c.a. Tuttavia, tale descrizione potrebbe riguardare anche pareti in c.a. di notevole estensione. La differenza essenziale tra le due situazioni è che nel secondo caso è sicuramente presente una casseratura che, almeno alle brevissime stagionature, “protegge” il calcestruzzo giovane dalle elevate temperature estive.
Temperature più elevate (con insolazione diretta magari) aumentano infatti la velocità di evaporazione dell’acqua dai getti “freschi”, esponendo il materiale a fessurazioni, porosità elevate, penalizzazione delle prestazioni fisiche e meccaniche. Nel caso dei pavimenti, il problema della rapida evaporazione di acqua dal getto è aggravato dalla totale assenza di casseratura ed il calcestruzzo risulta quindi esposto all’ambiente esterno per diverse ore, dal getto fino alla completa finitura.

Esistono delle soluzioni?
Pasqualini Alessandro
Diverse sono le soluzioni, più o meno utilizzate, utili ad evitare una precoce disidratazione del materiale:
- Bagnatura continua delle superfici con acqua. Tecnica efficace ma dispendiosa da realizzare soprattutto in climi caldi in quanto richiede il continuo intervento e monitoraggio da parte degli operatori di cantiere ed in talune circostanze di difficile realizzo.
- Applicazione di TNT bagnati ricoperti da teli in polietilene. Scelta performante, idonea nella realizzazione delle pavimentazioni industriali. Non indicata per strutture verticali.
- Applicazione a spruzzo di prodotti stagionanti (“curing compound”). Soluzione semplice, versatile ed affidabile che può essere applicata, in generale, su tutte le tipologie strutturali. Essi sono infatti adeguati sia per getti molto estesi (pensiamo alle pavimentazioni o strutture verticali quali pareti o muri) e sia per getti più contenuti magari caratterizzati da una geometria più o meno complessa (es. travi, pilasti, loro connessioni, ecc..), per i quali l’applicazione dei teli o la bagnatura continua possono risultare di non facile applicazione/gestione.
In merito alla possibilità di optare per soluzioni di stagionatura differenti a seconda del tipo di opera, in base a quanto descritto in precedenza si possono esprimere i seguenti pareri:
- In presenza di getti piuttosto contenuti (da un punto di vista di superficie), tutte le tipologie di stagionatura risultano tutto sommato adeguate.
- Nel caso di getti piuttosto estesi, si raccomanda l’impiego di soluzioni che non comportino il periodico intervento di manovalanza, in modo da scongiurare eventuali dimenticanze e/o interventi disomogenei sulle superfici.
- L’impiego di agenti stagionanti rappresenta, in generale, una soluzione piuttosto versatile indipendentemente dalla dimensione dei getti. Inoltre, il rapporto costi/benefici, o meglio, costi/qualità dei risultati, è certamente favorevole se confrontato con quello associabile agli altri sistemi di stagionatura.
Calcestruzzo e prodotti antievaporanti
Come e quando vanno applicati?
Pasqualini Alessandro
L’applicazione di prodotti stagionanti (“Curing Compound”), o le tecniche alternative di stagionatura appena citate, rappresentano una fase necessaria, soprattutto in clima estivo, per il completamento del ciclo costruttivo di un’opera in calcestruzzo.
Questi prodotti in particolare, sono facilmente applicabili a spruzzo sulla superficie del calcestruzzo subito dopo l’inizio della presa e possono avere meccanismi di funzionamento diversi.
Ad esempio, il prodotto CURING WF di General Admixtures, di particolare efficacia una volta applicato uniformemente sulle superfici, forma un film protettivo trasparente sulla superficie (barriera fisica).
Mentre il prodotto CURING S di General Admixtures reagisce con acqua e cemento formando una pellicola microcristallina che aderisce perfettamente alla superficie trattata. Quest’ultima non interferisce sull’adesione con altri trattamenti o rivestimenti ricoprenti e limita il ritiro dovuto all’essiccazione, permettendo nel contempo il corretto sviluppo della resistenza meccanica corticale del calcestruzzo.
È fondamentale chiarire che, nel caso delle pavimentazioni, i prodotti stagionanti non devono essere nebulizzati in presenza di bleeding. Qualora dovesse essere presente acqua di risalita in superficie, l’applicazione dovrà essere rimandata al termine dell’evaporazione dell’acqua di essudamento.
Gli antievaporanti sono sufficienti o serve anche altro?
Pasqualini Alessandro
La soluzione più efficace da adottare è quella di abbinare l’uso di agenti stagionanti all’impiego di un calcestruzzo a prestazione garantita, additivato durante la fase di preconfezionamento con gli Shrinkage Reducing Admixtures, meglio noti con l’acronimo SRA, tipo il GINIUS SRA1 di General Admixtures. Essi svolgono sostanzialmente una triplice azione:
- Riducono, a parità di condizioni esterne, la contrazione da ritiro igrometrico. Rispetto ad un calcestruzzo “ordinario”, il ritiro igrometrico risulta ridotto fino al 50%.
- Esplicano una azione “auto-stagionante” nel calcestruzzo. La loro presenza, quindi, limita l’evaporazione dell’acqua dal conglomerato, migliorando anche il mantenimento della lavorabilità in clima caldo.
- In presenza di agenti espansivi, come l’EXPANCOLL di General Admixtures, utilizzati per il confezionamento di calcestruzzi a ritiro compensato (ormai ben noti nel mondo delle pavimentazioni industriali per la possibilità di realizzare estese campiture senza alcun giunto di contrazione), il GINIUS SRA1 ne favorisce la corretta idratazione e quindi l’adeguato sviluppo dell’espansione necessaria a compensare la contrazione da ritiro.
Certamente, non si può non concludere la discussione senza sottolineare un aspetto fondamentale: ai sistemi di protezione sopramenzionati, con particolare riferimento agli antievaporanti
CURING S e CURING WF, devono sempre essere associati, soprattutto quando si parla di getti in climi estivi, ulteriori provvedimenti finalizzati ad attenuare l’effetto delle “avverse” condizioni climatiche che favoriscono l’evaporazione dell’acqua dai getti: elevate temperature, insolazione diretta, ventilazione. Sarà quindi opportuno, ad esempio, realizzare i getti nel tardo pomeriggio, in maniera tale che il pavimento possa godere del favore della notte per poter stagionare in maniera più adeguata durante le sue prime ore di vita (le più importanti) oppure realizzare, quando necessario e possibile, opportune protezioni antivento.
Pavimentazione esterna per logistica ad alta resistenza: quali scelte preventive se si getta in estate?
Quali sono le scelte preventive che si dovrebbero fare sul calcestruzzo?
Pasqualini Alessandro
Le principali accortezze che possono migliorare sensibilmente la buona riuscita della posa in opera di una struttura come quella presentata sono le seguenti:
- Impiegare di un additivo superfluidificante che sia formulato per le elevate temperature e in maniera specifica per la realizzazione di pavimentazioni. Tale additivo, come il PRIMIUM FLOOR 290 di General Admixtures, è concepito per:
- Consentire di ridurre il adeguatamente il rapporto a/c, in maniera da coniugare la necessaria lavorabilità con le elevate prestazioni richieste. Inoltre, la riduzione dell’acqua di impasto attenuerà il bleeding e, di conseguenza, il fenomeno dell’evaporazione, e consentirà di ottimizzare, a parità di a/c, il contenuto di cemento e quindi il ritiro igrometrico.
- Favorire un adeguato mantenimento della lavorabilità.
- Regolare adeguatamente i tempi di presa ed indurimento del calcestruzzo, in modo da consentire la posa in opera e la finitura dei getti nel rispetto delle tempistiche previste.
- Impiegare fibre polipropileniche, tipo FIBERCOLL FLEX 40 o FIBERCOLL TOP di G.A., utili a distribuire nel conglomerato cementizio una sorta di “armatura diffusa” capace di intercettare ogni eventuale microcavillatura che dovesse formarsi.
- Impiegare additivi Riduttori di Ritiro (Shrinkage Reducing Admixture) tipo GINIUS SRA1 di General Admixtures. In modo da ridurre ritiro igrometrico (fino al 50% rispetto ad un calcestruzzo non additivato) e favorire una azione auto-stagionante del calcestruzzo. Potendo contare su una migliore stagionatura del conglomerato, la parte corticale della pavimentazione, che nel caso in esame sarà particolarmente sollecitata, risulterà più compatta, resistente e durevole.
- Impiegare trattamenti superficiali per incrementare la resistenza all’usura ed all’abrasione della pavimentazione attraverso prodotti impregnanti quali il FLOOR PROTECT 300. Applicato mediante un comune nebulizzatore sulla superficie al termine della stagionatura umida (almeno dopo 14 gg dalla posa in opera del pavimento), reagisce con il Ca(OH)2 presente nella matrice cementizia (nei primi millimetri di spessore del calcestruzzo), formando silicati idrati insolubili (C-S-H) che riducono le porosità superficiali del materiale, incrementandone notevolmente le prestazioni fisiche, meccaniche e di durabilità. Tali prodotti possono essere inseriti nel Piano di Manutenzione della pavimentazione, in modo tale che, attraverso interventi periodici programmati, si possa contribuire alla conservazione delle prestazioni nel tempo.
- Impiegare aggregati alluvionali caratterizzati da un diametro massimo paria a 32 mm. Tale scelta consentirà di ridurre la superficie specifica dell’aggregato e quindi il volume di pasta necessario a conseguire una specifica lavorabilità. Potranno quindi essere ottimizzati i contenuti di cemento, da i quali dipende fortemente l’entità del ritiro igrometrico e quindi del rischio di fessurazione.
Quali sono le scelte preventive che si dovrebbero fare sulla stagionatura?
Pasqualini Alessandro
Si ritiene che, proprio in questo caso specifico sia fondamentale la scelta della tecnica di maturazione più adeguata. Nel caso di calcestruzzi ad elevate prestazioni caratterizzati da valori del rapporto acqua/cemento molto ridotti, oltre al fenomeno del ritiro igrometrico occorre prestare particolare attenzione a quello del cosiddetto ritiro autogeno. Quest’ultimo deriva da un fenomeno di auto-essiccamento della pasta cementizia provocato, a causa del rapporto a/c molto basso, dalla mancanza di acqua nei micropori.
Per questo, la protezione dei getti con teli in plastica o prodotti antievaporanti, non sono utili ad evitare la potenziale fessurazione da ritiro autogeno. Dovrà quindi essere programmata ed eseguita una accurata bagnatura della pavimentazione (immediatamente dopo la presa del calcestruzzo), proseguendo in tale attività per almeno 3 giorni. In assenza di questa procedura, certamente efficace ma piuttosto laboriosa, l’impiego del già citato additivo auto-stagionante e riduttore di ritiro GINIUS SRA1 potrà contribuire all’attenuazione del rischio di fessurazioni da ritiro autogeno (e igrometrico).
Pavimentazione in calcestruzzo drenante: stagionatura e prodotti di protezione se gettata in estate
Come va stagionata?
Pasqualini Alessandro
Le pavimentazioni “drenanti” sono realizzate con calcestruzzo dall’elevato volume di vuoti, utile a favorire il drenaggio dell’acqua verso gli strati inferiori. Proprio a causa di questa sua “struttura aperta”, il calcestruzzo drenante è maggiormente predisposto alla perdita di acqua (essiccazione) subito dopo la sua posa in opera. In condizioni particolarmente severe, quali quelle tipiche della stagione calda, la stagionatura di tali manufatti dovrebbe quindi cominciare immediatamente dopo la stesa del calcestruzzo (non più tardi di 20 minuti), quando il materiale mostra ancora lucentezza superficiale. Se quest’ultima si fosse attenuata, occorrerà ripristinarla immediatamente nebulizzando acqua sulla superficie.
La stagionatura umida dovrà avvenire, per almeno 7 giorni, applicando teli in polietilene in aderenza alla superficie. Tali teli, di adeguato spessore (almeno 0.15 mm), dovranno essere disposti in maniera da rispettare una adeguata sovrapposizione (almeno 30 cm), opportunamente vincolati a terra in modo da evitare un loro spostamento.
Ci sono prodotti speciali?
Pasqualini Alessandro
Al termine della stagionatura, l’applicazione a spruzzo di silicati cristallizzanti a base di litio come il FLOOR PROTECT 300 di G.A. potrà migliorare sensibilmente la consistenza della lastra in superficie. Questi prodotti, infatti, trasformando il “dilavabile” Ca(OH)2 in fibre stabili di silicati idrati di calcio (C-S-H), contribuiranno a migliorare il legame tra gli aggregati in superficie, attenuando l’annoso fenomeno dello sgranamento superficiale (problematica purtroppo frequente di questa tipologia di pavimentazione, soprattutto in conseguenza di una errata/inadeguata stagionatura umida).
Quali consigli per l’impresa applicatrice?
Pasqualini Alessandro
A costo di apparire ripetitivi, il consiglio è quello di eseguire la stagionatura e maturazione del materiale in maniera estremamente attenta e rapida, in quanto, come detto, questo tipo di materiale è particolarmente predisposto alla perdita di acqua per evaporazione e quindi all’indebolimento corticale del “legame” tra pasta cementizia ed aggregato. Sbagliare la stagionatura significa, per questi pavimenti, rischiare di ottenere una superficie poco coesa con diffusi fenomeni di sbrecciamento.
Getto di calcestruzzo per strutture verticali in estate
È sufficiente mantenere le casseforme in opera per più tempo?
Pasqualini Alessandro
Tutte le strutture gettate entro cassero possono beneficiare di una valida protezione nei riguardi della prematura evaporazione dell’acqua dal calcestruzzo a patto che le casseforme siano realizzate in materiale impermeabile quali acciaio, cartone con membrana interna in polietilene, pvc, polistirolo, oppure in compensato di legno trattato con resine. In generale, quindi, indipendentemente dal tempo di permanenza in opera, le casseforme realizzate ad esempio in legname “standard”, non offrono totale garanzia di “protezione”, in quanto tale materiale risulta piuttosto poroso e, soprattutto in climi caldi e soleggiati, possono assorbire acqua dalla superficie del calcestruzzo per poi veicolarla in atmosfera. Se invece i materiali sono adeguati, il mantenimento delle casseforme in opera è certamente un espediente molto valido per poter maturare correttamente i getti nei loro primi giorni di “vita”. A tale riguardo, la permanenza dei casseri non dovrebbe mai essere inferiore ai 3 giorni e, in generale, non occorre che sia superiore ai 10 giorni.
Ci sono soluzioni tecniche di supporto che possono permettere di evitare questo protrarsi dello stazionamento delle casseforme?
Pasqualini Alessandro
Il mantenimento protratto dei casseri viene molte volte osteggiato dalle imprese a causa della impossibilità di poter riutilizzare velocemente i pannelli per proseguire con i lavori. Si ritiene che, per le strutture casserate in genere, l’unica alternativa valida alla protezione offerta dai casseri (di materiale adeguato), sia l’impiego dei prodotti stagionanti, tipo CURING S o CURING WF di General Admixtures.
Questo per i seguenti motivi:
- Efficacia della stagionatura. L’applicazione di tali prodotti mediante nebulizzazione, consente di realizzare sulla superficie del calcestruzzo una barriera impermeabile stabile per alcuni giorni. Questa impedisce l’evaporazione dell’acqua dai getti in atmosfera e quindi riduce drasticamente la possibilità che si presentino fessurazioni da ritiro o che il copriferro possa risultare poroso.
- Semplicità nell’applicazione. Questa avviene mediante semplici pompe airless, pertanto non è richiesta alcuna competenza specifica all’applicatore.
- Applicazione una tantum. I prodotti vengono applicati subito dopo lo scassero e non è necessario, in genere, intervenire successivamente con nuove applicazioni. Al contrario, la tecnica della bagnatura intermittente delle superfici può fallire, semplicemente a causa di una potenziale “inaffidabilità” delle maestranze nel rispettare i tempi di bagnatura.
- Ottimale per elementi verticali o di forma generica. Per gli elementi casserati l’applicazione di teli impermeabili o di iuta è di fatto spesso complicata, sia perché gli elementi sono generalmente a sviluppo verticale (es. pilastri, setti) e sia perché le forme sono spesso complesse e non consentono l’applicazione di teli in aderenza (es. travi di un impalcato).
Per il caso specifico dei pilastri si vuole porre l’attenzione su una tecnica di maturazione che alla semplicità associa l’elevata efficacia. Essendo i pilastri elementi di fatto “isolati”, nel senso che tutta la loro superficie laterale è libera (almeno nelle prima fasi costruttive dell’opera) ed il perimetro della loro sezione è in genere limitato, essi posso essere facilmente rivestiti, subito dopo le operazioni di scassero, con una comune pellicola di cellophane. Tale operazione, realizzabile in pochi minuti, consente di fatto di impermeabilizzare completamente la superficie dell’elemento, preservandola dall’evaporazione di acqua. Inoltre, una volta applicato, lo strato di cellophane potrà essere lasciato in opera a tempo indefinito, non comportando alcuna interferenza con il proseguimento dei lavori. Tale tecnica viene spesso utilizzata per la corretta maturazione di malte o betoncini strutturali, nonché di microcalcestruzzi fibrorinforzati ad elevate prestazioni, come il COMPOSITE M130 di General Admixtures, utilizzati per il ripristino corticale, la riparazione o il rinforzo di pilastri in c.a. (camicie in basso spessore)
Attesa del calcestruzzo in cantiere a 38 °C
Pasqualini Alessandro
Innanzitutto è doverosa una premessa importante. In generale le operazioni di getto del calcestruzzo non dovrebbero essere eseguite quando la temperatura del materiale supera il 35 °C, come riportato, ad esempio, nelle Linee guida “per la messa in opera del calcestruzzo strutturale e per la valutazione delle caratteristiche meccaniche del calcestruzzo indurito mediante prove non distruttive” edite dal STC del Consiglio Superiore dei Lavori Pubblici. Detto questo, qualora cause di forza maggiore non consentano di rinviare i getti, certamente dovranno essere attuate una serie di accortezze utili a mitigare gli effetti negativi che le elevate temperature possono avere sul calcestruzzo, sia allo stato fresco che indurito.
In generale, l’adeguata gestione delle fasi di lavorazione dovrebbe evitare che il calcestruzzo giunto in cantiere rimanga troppo tempo in attesa prima che questo venga posto in opera. Tale auspicio è ancora più sentito nella stagione calda (o estremamente calda) quando il mantenimento di lavorabilità del materiale viene messo a dura prova dalle elevate temperature.
L’impiego di specifici additivi superfluidificanti a base acrilica, come ad esempio il PRIMIUM HR 350 di General Admixtures, formulati proprio per esaltare la capacità di mantenimento di lavorabilità in condizioni “estreme”, aiuta molto, in questi casi, ad attenuare fortemente indesiderate perdite di lavorabilità. Inoltre, in condizioni particolarmente estreme, può essere necessario associare ai superfluidificanti ora richiamati anche specifici additivi ritardanti, tipo RETARD G2, che adeguatamente dosati nell’impasto consentono di regolare in maniera adeguata i tempi di presa ed indurimento del materiale.
Calcestruzzo e clima caldo: cosa fare nel caso di pavimenti esterni da non rivestire?
Pasqualini Alessandro
I problemi principali possono essere legati a:
- Difficoltà nella corretta realizzazione dello spolvero superficiale: la sua applicazione deve infatti avvenire nel rispetto di tempistiche precise, allorquando il pavimento è “calpestabile” ma l’indurimento non sia ancora avviato. In presenza di temperature così elevate, il rischio è quello di non riuscire ad inglobare lo spolvero nella matrice del calcestruzzo con il rischio di successive delaminazioni superficiali. In tali situazioni, la sostituzione dello spolvero superficiale con una applicazione a spruzzo (sulla pavimentazione stagionata) di silicati cristallizzanti, come ad esempio FLOOR PROTECT 300 (a base di litio) o FLOOR PROTECT 400 (a base di sodio), consentirà di conseguire comunque una superficie molto resistente ad urti ed abrasioni, con il vantaggio di evitare una lavorazione “a rischio” come quella dell’applicazione dello spolvero.
- Difficoltà di stagionare efficacemente da subito il materiale: con temperature così elevate, il rischio di una rapida essiccazione del calcestruzzo appena gettato è concreto. La protezione dovrà quindi avvenire sin da subito. Per fare questo, se la pavimentazione è stata posta in opera con, ad esempio, la laser screed, la consistenza della superficie può essere tale da consentire l’applicazione immediata di teli in polietilene. Se invece il pavimento è stato gettato con calcestruzzo fluido o superfluido, le cose si complicano moltissimo, giungendo quasi ad una situazione “critica”. In questo caso, infatti, i teli non possono essere applicati (il calcestruzzo è troppo fresco e deformabile) e l’unica soluzione potrebbe essere quella di applicare immediatamente prodotti stagionanti (Curing compound). Tuttavia, questa tempistica applicativa rischia di penalizzare molto la prestazione dei prodotti, che tenderebbero ad essere “dilavati” dalla notevole umidità del calcestruzzo fresco. In presenza di bleeding, poi, tali applicazioni sarebbero di fatto totalmente inefficaci. È evidente quindi che per quest’ultima situazione ora descritta non si può che raccomandare fortemente di eseguire i getti solo a partire dal tardo pomeriggio o, se possibile, durante le ore notturne.
Cosa fare nel caso di pavimenti di calcestruzzo esterni da rivestire con resina?
Pasqualini Alessandro
I problemi principali possono essere connessi a:
- Realizzazione della pavimentazione in calcestruzzo che fungerà da “supporto” al rivestimento;
- Esecuzione del rivestimento (applicazione della resina).
Per il primo aspetto, si rimanda evidentemente a quanto visto in precedenza. Si sottolinea che una errata/incompleta maturazione umida può comportare, oltre che problemi di fessurazione, anche una concreta penalizzazione delle caratteristiche di resistenza e porosità del calcestruzzo corticale e questo, nel caso dei pavimenti da rivestire con resina, si può ripercuotere sull’aderenza rivestimento-calcestruzzo (in ogni caso è sempre buona regola prevedere una preliminare carteggiatura della superficie del supporto che ne aumenti la rugosità).
Per il secondo aspetto, quello legato all’applicazione del rivestimento (es. resine superficiali), la temperatura del supporto è un parametro fondamentale per la corretta riuscita dell’intervento. Temperature troppo elevate comportano forti riduzioni dei tempi di lavorabilità della resina e questo può complicare notevolmente, o addirittura rendere impossibile, la sua posa in opera.
In generale, l’applicazione di una resina non può essere intrapresa quando la temperatura ambientale e/o della superficie del supporto è inferiore a +10 °C o superiore a +35 °C (salvo diverse indicazioni da parte del Fornitore della resina).
In periodi estivi, come quello oggetto della discussione, non potendo rinviare le lavorazioni a periodi della giornata più freschi (in particolare all’alba, quando la temperatura del supporto ha potuto godere delle minori temperature per tutta la notte), occorrerà utilizzare, se il ciclo di lavorazione lo consente, indurenti meno reattivi, caratterizzati da tempi di lavorabilità più lunghi, oppure modificare le abitudini di lavoro impastando quantitativi inferiori e applicando il prodotto, se possibile, più velocemente.
Inoltre, è fondamentale scegliere, per lo stoccaggio dei materiali, un sito che d’estate risulti fresco, in modo da mantenere la temperatura del prodotto su valori ideali variabili tra +15 °C e +20 °C. Andrà inoltre valutata l’umidità del supporto prima dell’applicazione della resina, verificando che questa si attesti a valori inferiori al 4% (al fine di evitare successivi fenomeni di sbollature). In giornate molto calde, tuttavia, potrebbero verificarsi valori di U.R. ambientale molto elevati che ostacolerebbero il conseguimento di tale condizione.
Cosa fare nel caso di getti di strutture quali travi e pilastri?
Pasqualini Alessandro
È fondamentale limitare la temperatura del calcestruzzo per evitare sviluppi di resistenza troppo accelerati nel breve periodo che porterebbero a non trascurabili penalizzazioni di resistenza a lungo termine (28 giorni). Tali penalizzazioni, nel caso di elementi pilastro o trave sono, in generale, assolutamente intollerabili.
Si consiglia quindi di:
- Lasciare l’autobetoniera in attesa al fresco e, se possibile, bagnare costantemente il tamburo con acqua fresca, in modo da evitare il surriscaldamento del materiale;
- Poco prima dell’esecuzione dei getti, bagnare le casseforme con acqua fredda, in modo da aiutare a ridurre la temperatura del calcestruzzo che sarà gettato all’interno dei casseri;
- Prima del getto proteggere le carpenterie dall’irraggiamento diretto e, se possibile, avvolgerle con teli di iuta bagnati di frequente. Rimuovete tali protezioni solo poco tempo prima dei getti.
- Impiegare superfluidificanti specifici, come ad esempio il PRIMIUM HR 350 di General Admixtures. Grazie ad essi il materiale non subirà sviluppi di resistenza troppo rapidi nel brevissimo periodo e quindi le prestazioni a lungo tempo saranno maggiormente preservate. Attenzione però. Allungare i tempi di presa e di indurimento può determinare un incremento dell’evaporazione di acqua, quindi, si ribadisce il consiglio di prevedere sempre l’impiego di additivi auto-stagionanti come il GINIUS SRA1 che tutelino maggiormente il materiale nei confronti della prematura essiccazione.
Cosa fare nel caso di getti massivi?
Pasqualini Alessandro
L’elevata temperatura ambientale concomitante alle operazioni di getto determina un aumento della temperatura del calcestruzzo allo stato fresco. Nel caso dei getti massivi, questa situazione risulta penalizzante in quanto alla temperatura “iniziale” del calcestruzzo già elevata si va a sommare l’incremento di temperatura derivante dalla idratazione del cemento. Il risultato è quello di ottenere un innalzamento della temperatura di picco nel nucleo del getto, con tutte le conseguenze ben note. Per questo motivo, anche nel caso di getti massivi, il consiglio principale è quello di confezionare il materiale e metterlo in opera durante le ore notturne, in maniera da ridurre la temperatura iniziale del calcestruzzo. Trovandosi costretti a realizzare in ogni caso i getti in presenza di temperature ambientali di circa 38°C, le principali cautele che possono attuarsi sono:
- Prima del getto tenere in ombra i casseri e (in particolare) le armature metalliche, in modo da limitare la loro temperatura.
- Lasciare l’autobetoniera in attesa al fresco e, se possibile, bagnare costantemente il tamburo con acqua fresca, in modo da evitare il surriscaldamento del materiale.
- Prima del getto, bagnare abbondantemente sia i casseri che le armature con acqua fredda, in modo che il calcestruzzo fresco possa ridurre la sua temperatura iniziale.
- Limitare quanto più possibile il tempo di attesa del calcestruzzo in cantiere.
- In caso di temperature molto elevate, confezionare il calcestruzzo inserendo del ghiaccio in parziale sostituzione dell’acqua di impasto.
- Presso l’impianto di preconfezionamento, evitare l’insolazione diretta delle materie prime costituenti il calcestruzzo.
Tali accortezze, se pur non totalmente risolutive della condizione estrema di lavoro, consentiranno di abbassare la temperatura del calcestruzzo di diversi gradi centigradi e quindi, di ridurre di altrettanti gradi la temperatura di picco raggiunta nel nucleo del getto. L’altro obbiettivo essenziale da perseguire e quello di ridurre i gradienti termici tra nucleo e periferia. Questo potrà essere raggiunto adottando una opportuna coibentazione dei casseri, da mantenere in opera per almeno 7 – 10 giorni, a seconda dello spessore della struttura che si sta realizzando.
Infine, per quanto attiene a specifiche precauzioni da adottare nell’ambito del mix-design, esse sono ben note e sono valide anche nel caso di temperature ambientali “ordinarie”:
- Adottare specifici cementi a sviluppo di calore molto ridotto (par. 11.2.9.2 del DM 17 gennaio 2018, cementi speciali conformi a UNI EN 14216).
- Limitare quanto più possibile il contenuto di cemento, ricorrendo anche a prescrizione della resistenza a compressione a tempi di maturazione maggiori dei canonici 28 giorni (par. 11.2.1 del DM 17 gennaio 2018).
- Fare largo uso di aggiunte minerali pozzolaniche (tipo cenere volante MICRO-POZZ PFA di General Admixtures) in parziale sostituzione del cemento.
- Impiegare specifici additivi superfluidificanti riduttori di acqua (nel caso in esame formulati per la stagione estiva, come il PRIMIUM HR 350 di General Admixtures), in modo da abbassare il contenuto di acqua e quindi, a parità di a/c, ottimizzare quello del cemento.
- Aumentare quanto più possibile il diametro massimo dell’aggregato, in maniera da ridurre la richiesta d’acqua efficace (Regola di Lyse).
Come fare per saperne di più?
Per ulteriori informazioni o approfondimenti,
CLICCA QUI e contatta il servizio assistenza di General Admixtures SpA oppure VISITA SITO

In ALLEGATO è disponibile l'articolo in formato PDF, per poterlo leggere con un'impaginazione migliore, stamparlo, salvarlo, condividerlo
SCARICALO ORA
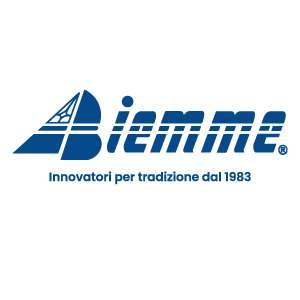
Calcestruzzo Armato
Esplora la guida completa sul calcestruzzo e sul calcestruzzo armato, due elementi fondamentali nell'edilizia. Scopri le composizioni, come l'integrazione di fibre metalliche e polimeriche, e le ultime innovazioni che migliorano le proprietà strutturali. Aggiorna le tue conoscenze sui materiali cementizi per una comprensione avanzata e applicazioni ottimali.
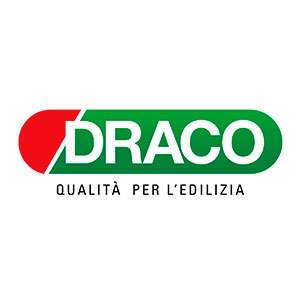
Pavimenti Industriali
Con il topic "pavimento industriale" vengono raccolti tutti gli articoli pubblicati sul Ingenio su queste tipologie di pavimentazioni in calcestruzzo e riguardanti la normativa, la progettazione, l'applicazione, l'innovazione tecnica, i casi studio, i controlli e i pareri degli esperti.
Condividi su: Facebook LinkedIn Twitter WhatsApp